Come attrezzatura importante nel campo dell'industria moderna, il compressore d'aria a vite svolge un ruolo vitale nel fornire aria compressa. Dalla trasformazione alimentare alla produzione di macchinari, dalla produzione farmaceutica alla sintesi chimica, il funzionamento stabile dei compressori d'aria a vite è una garanzia importante per garantire linee di produzione fluide e qualità del prodotto stabile. Tuttavia, come tutte le attrezzature meccaniche, anche i compressori d'aria a vite hanno vari problemi a causa dell'usura, dell'invecchiamento o del funzionamento improprio durante l'uso. Pertanto, la revisione e la manutenzione regolari non sono solo la chiave per prolungare la vita dell'attrezzatura, ma anche le misure necessarie per garantire la sicurezza e l'efficienza della produzione. Questo articolo discuterà profondamente la revisione e il processo di manutenzione del compressore d'aria a vite e ti porterà in questo mondo di manutenzione complesso e fine. Per favore, critica e correggimi.
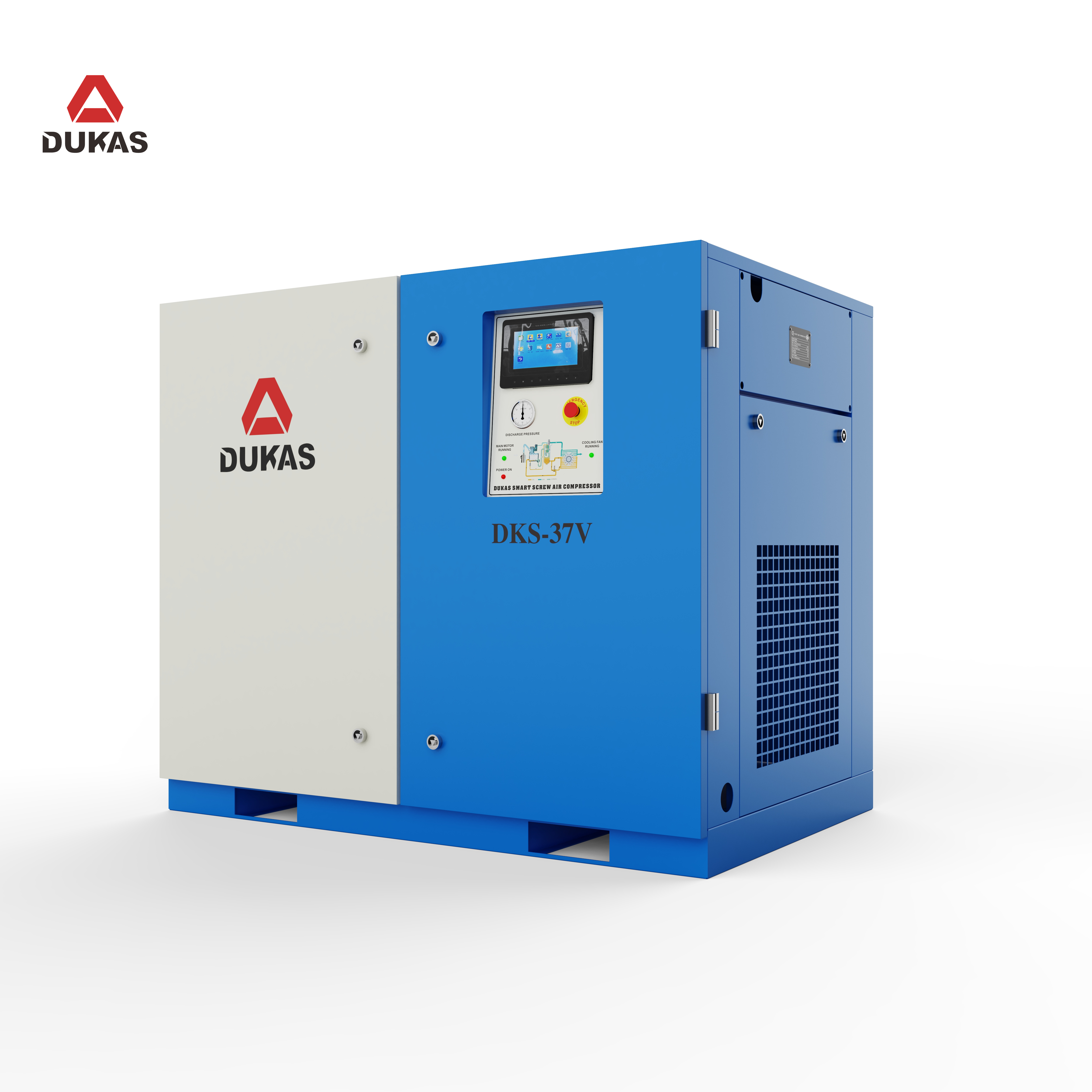
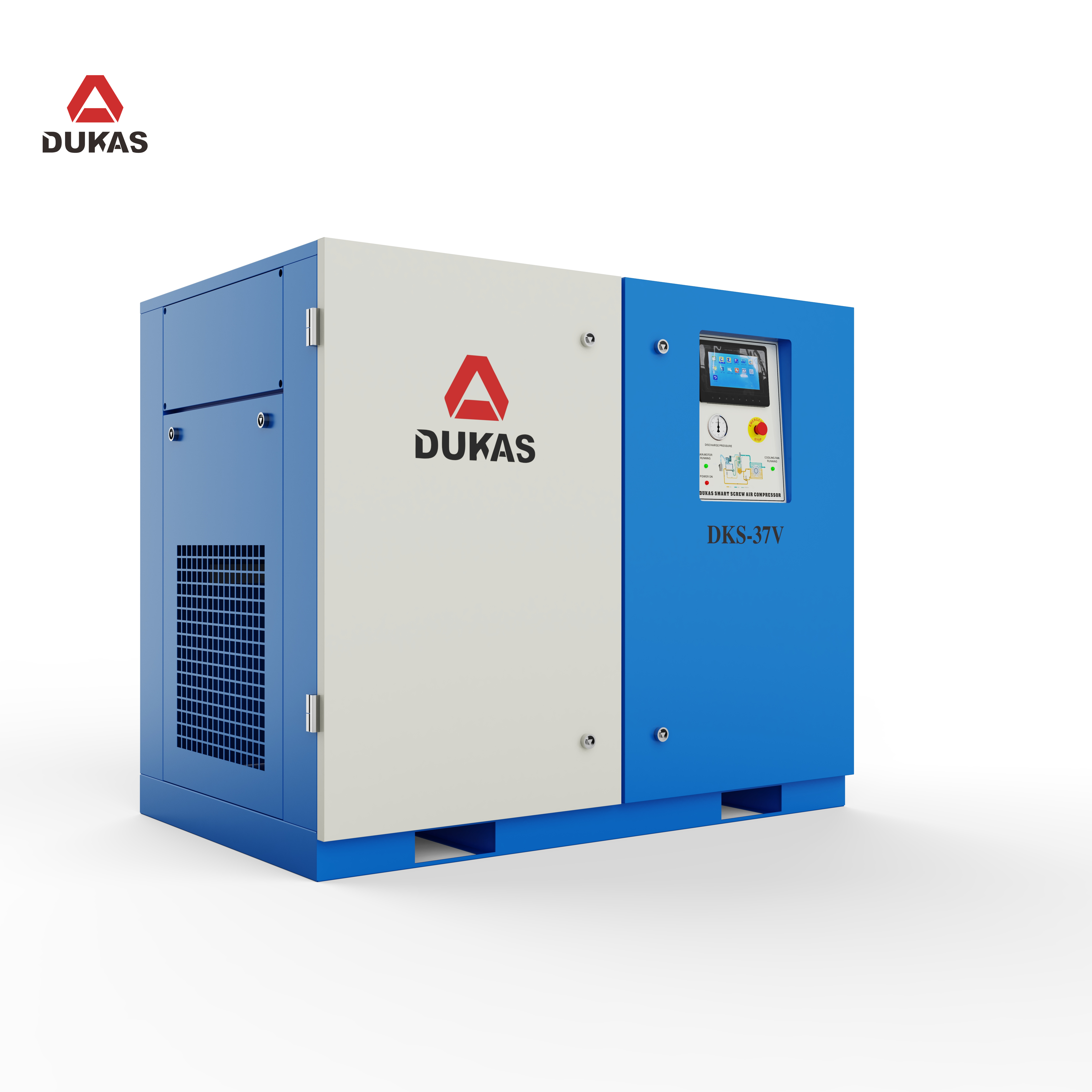
I. Il principio di lavoro e l'importanza del compressore d'aria a vite
Compressore d'aria a vite attraverso una coppia di configurazione parallela del rotore a spirale (rotore maschio e rotore femmina) nella rotazione ad alta velocità del guscio, aspirazione e compressione dell'aria e, in definitiva, scaricare il gas ad alta pressione. Questo design non ha solo le caratteristiche di una struttura semplice, un funzionamento regolare e un basso rumore, ma può anche fornire una produzione di gas stabile in un ampio intervallo di pressione, che è molto adatto per applicazioni industriali che richiedono una fornitura di gas continuo.
La sua importanza si riflette in:Rispetto al compressore d'aria a pistoni, il compressore d'aria a vite consuma meno energia sotto la stessa pressione, il che aiuta a ridurre i costi di produzione.
Stabile e affidabile:La progettazione della vite riduce le vibrazioni e l'usura e migliora la stabilità e l'affidabilità dell'attrezzatura.
Facile da mantenere:Il design modulare rende la manutenzione e la riparazione più comoda, riducendo i tempi di inattività.
Ii. Ispezione quotidiana: la prima linea di difesa per prevenire i guasti
L'ispezione giornaliera è la base della manutenzione del compressore dell'aria a vite, attraverso l'osservazione regolare, la registrazione e la semplice regolazione, può impedire efficacemente molti potenziali guasti.
Controllo del livello dell'olio:Assicurarsi che l'olio lubrificante sia all'interno della linea di scala specificata, troppo basso porterà a una lubrificazione insufficiente, troppo alta può causare una pressione anormale dell'olio.
Temperatura di scarico:In circostanze normali, la temperatura di scarico dovrebbe fluttuare all'interno dell'intervallo set, troppo in alto può indicare un guasto del sistema di raffreddamento o un blocco del filtro.
Ispezione delle perdite:Compreso separatore di carburante e vapore, collegamento del tubo e tenuta, qualsiasi perdita deve essere gestita in tempo per prevenire la miscela di petrolio e gas o caduta di pressione.
Vibrazione e rumore:Le vibrazioni e il rumore anormali sono spesso precursori di parti sciolte o usurate e devono essere controllati in tempo.
Iii. Manutenzione regolare: la chiave per mantenere le prestazioni delle attrezzature
La manutenzione regolare è il nucleo per garantire il funzionamento stabile a lungo termine del compressore d'aria a vite. A seconda della frequenza di utilizzo e dell'ambiente di lavoro, il ciclo di manutenzione può essere impostato su mensile, trimestrale o annuale.
Sostituire il filtro lubrificante per olio e olio:L'olio lubrificante non solo lubrifica il rotore e il cuscinetto, ma svolge anche un ruolo di raffreddamento e tenuta. Il filtro dell'olio è responsabile del filtraggio delle impurità e del mantenimento dell'olio. Si consiglia generalmente di sostituire ogni 2000-4000 ore di funzionamento.
Pulizia del sistema di raffreddamento:La superficie del dispositivo di raffreddamento è facile da accumulare polvere e sporco, influenzando l'effetto di dissipazione del calore, con conseguente aumento della temperatura di scarico. Utilizzare regolarmente aria compressa o speciale agente di pulizia per pulire il dispositivo di raffreddamento per mantenere le sue buone prestazioni di dissipazione del calore.
IV. Manutenzione professionale: soluzione approfondita di problemi complessi
Quando le ispezioni quotidiane e la manutenzione regolare non possono risolvere il problema, è richiesta una revisione professionale più approfondita. Questo di solito include quanto segue:
Regolazione del rotore e shell di regolazione:Dopo una lunga operazione di tempo, il divario tra il rotore e il guscio può aumentare, con conseguente declino dell'efficienza di compressione. Misurare e regolare il divario con strumenti professionali per ripristinare le prestazioni delle apparecchiature.
Manutenzione del sistema elettrico:Controllare i componenti elettrici come motore, avviamento, circuito di controllo, ecc., Per garantire che il collegamento elettrico sia affidabile, non si può cortocircuito e circuito aperto.
Calibrazione del sistema di controllo della pressione:L'accuratezza degli interruttori di pressione, dei sensori di pressione e di altri componenti influenzano direttamente la funzione di regolazione della pressione del compressore dell'aria. Controllare regolarmente per garantire un controllo di pressione stabile e affidabile.
Analisi delle vibrazioni e diagnosi dei guasti:L'uso dell'analizzatore di vibrazioni per analizzare lo spettro di frequenza del compressore d'aria, identificare fonti di vibrazione anormali, come squilibrio, parti sciolte o usurate, per fornire una base per una manutenzione accurata.
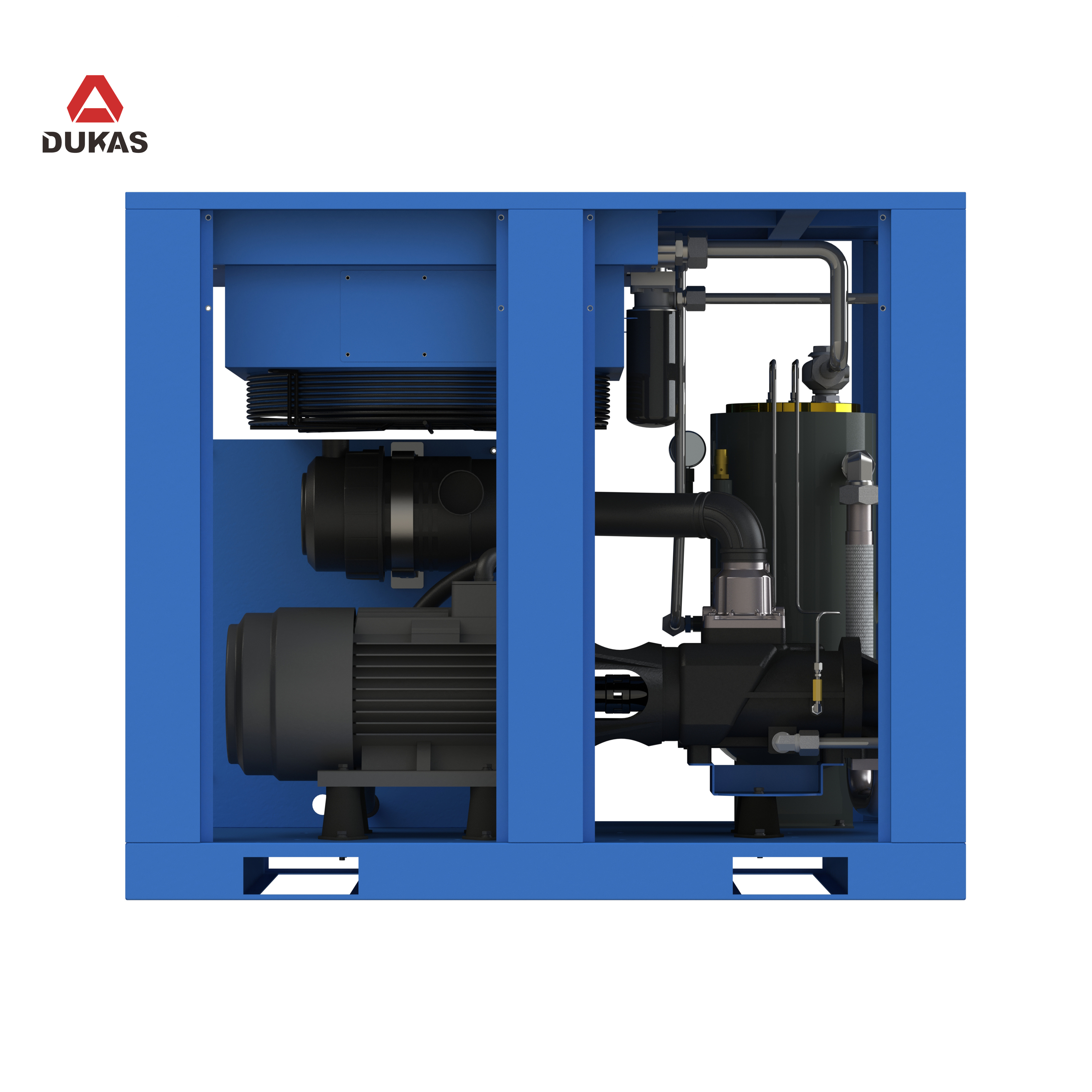
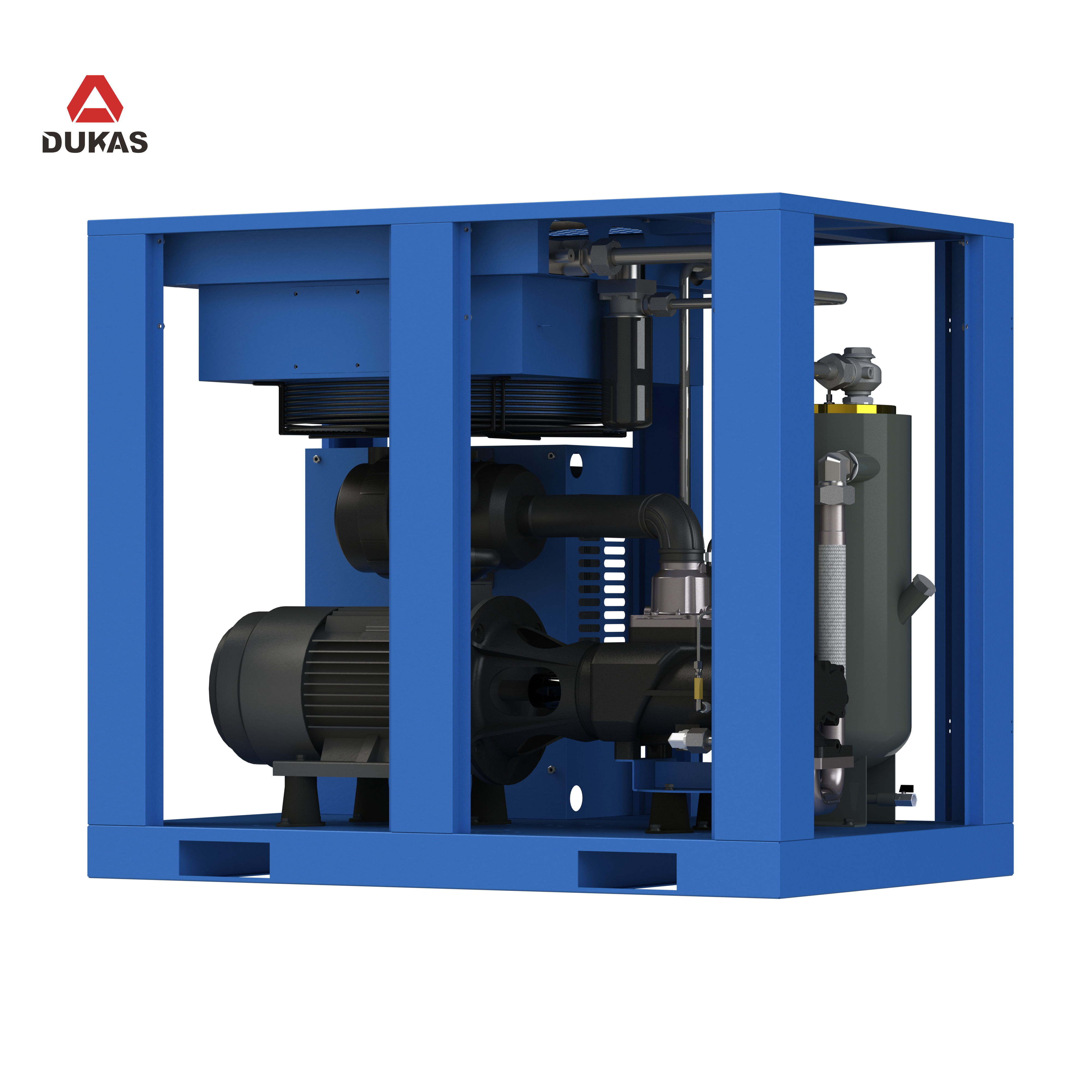
V. Manutenzione intelligente: tendenze future
Con lo sviluppo della tecnologia Internet of Things, la manutenzione intelligente è diventata gradualmente una nuova tendenza alla manutenzione del compressore d'aria a vite. Installando sensori e sistema di controllo di supervisione remoto, lo stato in servizio del compressore d'aria può essere monitorato in tempo reale.
Monitoraggio remoto:Gli utenti possono visualizzare a distanza lo stato di lavoro del compressore d'aria tramite un telefono cellulare o un computer, trovare anomalie in tempo e prendere misure.
Analisi dei dati:La grande quantità di dati raccolti dal sistema può essere analizzata attraverso algoritmi per prevedere la vita delle attrezzature, ottimizzare i piani di manutenzione e ridurre i tempi di inattività non pianificati.
Diagnosi intelligente:Combinato con l'intelligenza artificiale e la tecnologia di apprendimento automatico, il sistema può identificare automaticamente i tipi di guasto, fornire raccomandazioni di manutenzione e migliorare l'efficienza e l'accuratezza della manutenzione.
Vi. Considerazioni sulla sicurezza
Nella manutenzione e manutenzione dei compressori d'aria a vite, la sicurezza è sempre la prima priorità. Ecco alcune precauzioni di sicurezza di base:
Operazione di spegnimento:Assicurati di tagliare l'alimentazione prima della manutenzione e appendere la scheda di avvertimento "senza chiusura" per impedire l'inizio accidentale.
Rilascio di pressione:Prima della manutenzione, la pressione interna del compressore d'aria deve essere rilasciata per evitare ferite di gas ad alta pressione.
Protezione personale:Indossare attrezzature protettive adeguate, come caschi, occhiali protettivi, guanti, ecc., Per prevenire lesioni accidentali.
Seguire le procedure operative:Stendamente in conformità con il manuale dell'attrezzatura e le procedure operative per la manutenzione, per evitare l'abuso di danni alle attrezzature o lesioni personali.
La revisione e la manutenzione del compressore d'aria a vite sono un progetto sistematico, che coinvolge ispezioni quotidiane, manutenzione regolare, manutenzione professionale e manutenzione intelligente. Attraverso la gestione scientifica e un'attenta manutenzione, non solo può prolungare la vita delle attrezzature, migliorare l'efficienza operativa, ma può anche prevenire gli incidenti di sicurezza e garantire la sicurezza della produzione. Come pietra angolare della produzione industriale, la sana operazione dei compressori d'aria a vite merita più attenzione e sforzi. Andiamo di pari passo per esplorare metodi di manutenzione più efficienti e intelligenti e contribuiamo alla prosperità sostenuta della produzione industriale.
Tempo post: ottobre-31-2024